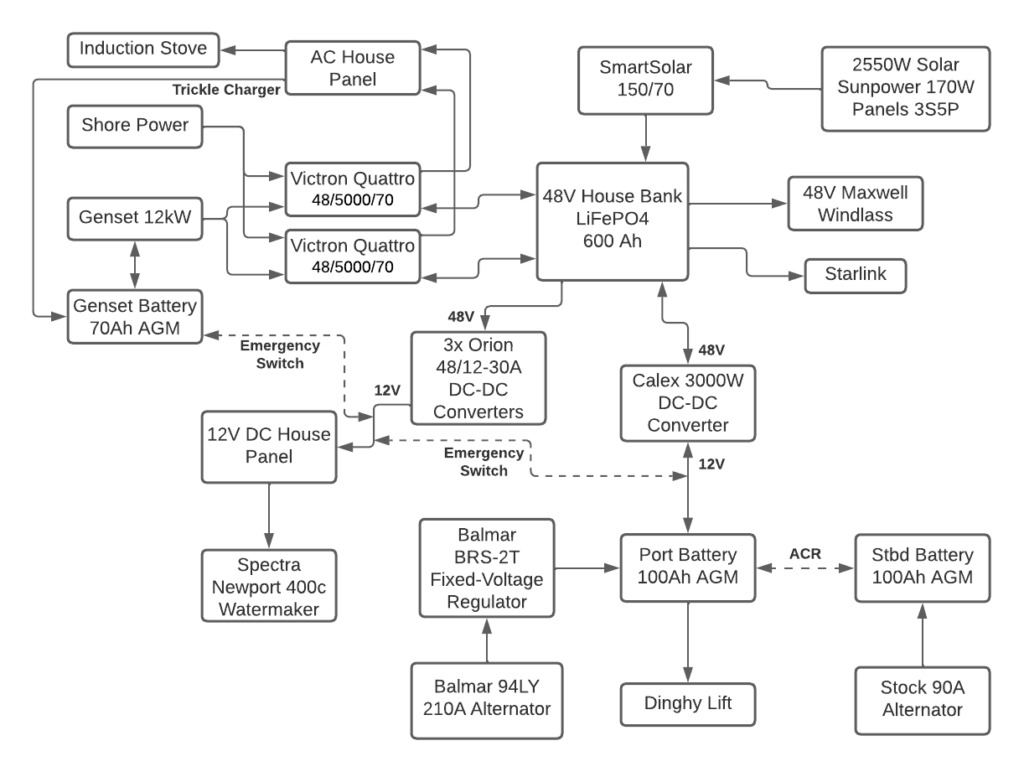
After over a year with the power system, and several tweaks, I'm at the point that I'm very happy with where things have landed, and figured it was time for an update. I also convinced a buddy boat of ours, Inquest, to do the same system, and we've been iterating with each other for the last year, which continues to be helpful. The original post from last year has more details on some of the history on why I went in this direction, if you're interested, but this post will be self-contained about the current system if you just want to know where we landed and the benefits.
Why 48V?
Let's get the basic question out of the way -- why the heck did I go with 48V? Most boats are 12V, with some natively 24V, but no one is doing 48V.
So, I don't just hate myself. I mean, obviously there's a little of that, but there are some tremendous advantages. If you look at off-grid systems for homes, they're all 48V, and my target was a lot closer to an off-grid home than a traditional "boat". And a lot of that is because converting back and forth between 48VDC and 120VAC is more efficient than to/from 12VDC. Similarly, for MPPT conversion off solar, downconverting to 48V is more efficient than all the way down to 12V. But even moreso, at house-level loads (i.e. regularly dipping into multiple kilowatts), the sizes of cables that you need to run to safely transfer power to/from 12V batteries is some combination of absurd, heavy, and somewhat dangerous.
Running 5kVA inverters with 12V batteries, we would need to run four 4/0 cables each for the positive and negative terminals (and, realistically, to be safe, another set of four for the ground), to each inverter -- they need around 1000 amps! With 48V batteries, we only need to run one each. Simpler, cheaper, far less inflexible cable to run around the boat, and generates much less heat at the terminals from 1/4 the amp load. I only have to run 4AWG wires from each battery to a common terminal, because 100 amps is more than they will ever see.
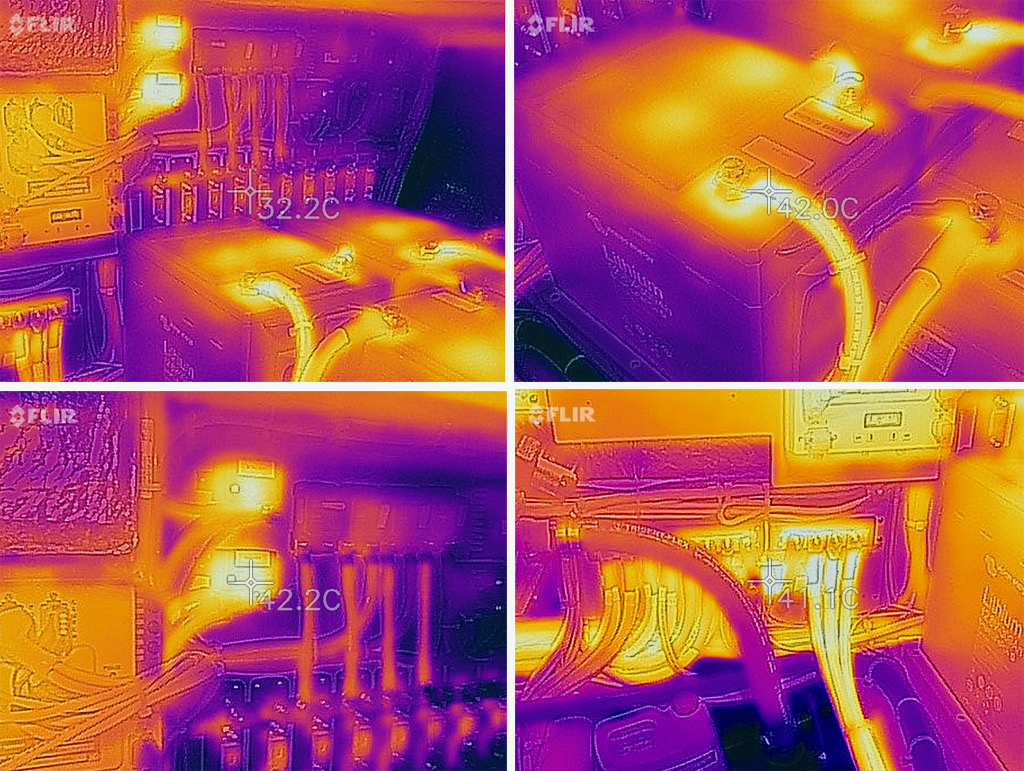
Finally, because of the low amp loads, battery chargers are simpler, cheaper, and more efficient. The same Quattro in 48V that charges at 70A will only do 120A at 24V or 200A at 12V (28% less power). Where I would need multiple MPPT chargers for my solar bank, I can instead use a single not-horribly-expensive one. Basically, everything in the 48V world is smaller, lighter, cheaper, and more efficient.
The downside to 48V, of course, is that you now need some way to feed your native 12V loads, but that turns out to not be too bad of a problem to solve, as I'll discuss later. That said, many devices are coming natively in 48V these days -- we have a native 48V windlass that plugs right into the house bank, POE networking gear uses 48V, there's a new generation of thrusters out that use 48V, and even watermakers are starting to come out in 48V. So it's becoming more standard in the marine world, but I would say it's still in the "bleeding edge" territory for most things.
Batteries
The core of the system is a 600Ah 48V house bank, made of six 100Ah BestGo packs in parallel. I picked these packs because they, at least at the time, were the best value in US-company-warranty-backed Lithium packs available (the 6 batteries were around 11k$ shipped to my door). They're also IP66-rated, which, on a boat, in a cabinet right under the A/C drip tray, next to a washer/dryer unit, and with the A/C water lines running literally right over them, seemed like a good idea. Lastly, Will Prowse did a teardown on them and found the build quality to be unmatched in their price range. They've been working flawlessly for me, with very little temperature buildup even under heavy charging and discharging.
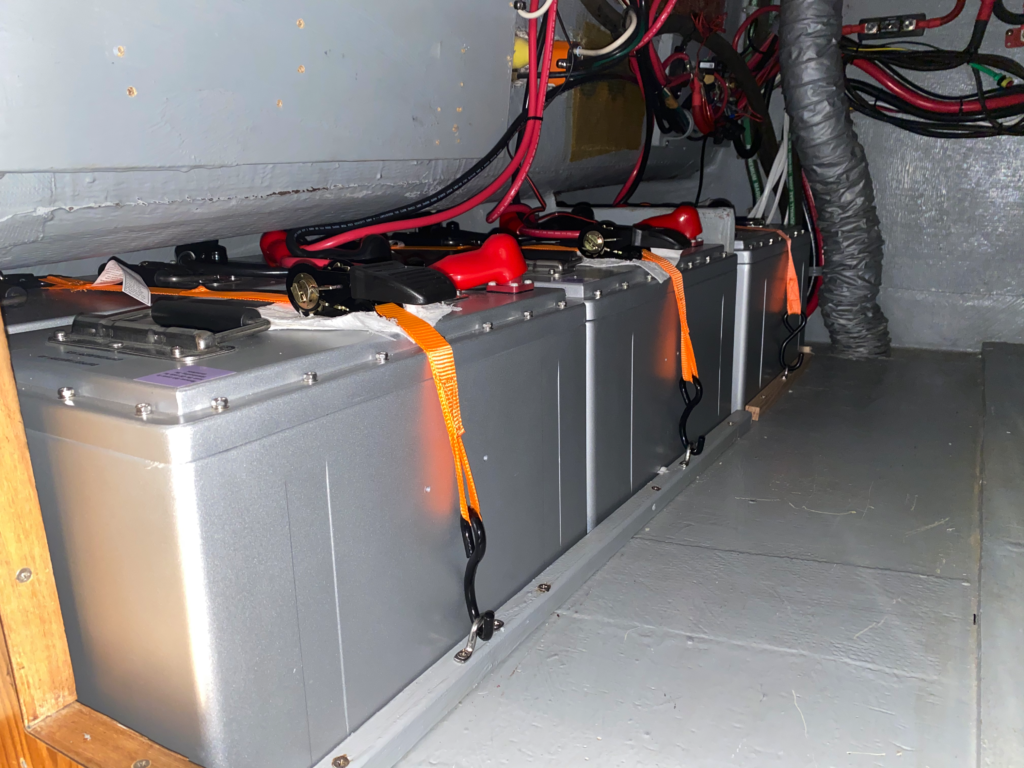
The batteries form the core power storage for the system, which is then mostly transformed to the other working voltages around the boat (12V and 120/240VAC), though more and more native 48V equipment is coming available. I've converted to a larger 48V windlass which pulls directly off the batteries and I'm running Starlink directly off POE from the batteries.
You can read about lithium batteries and what a different world they are than any sort of lead-based batteries, but you really have to live with them daily to appreciate how amazing they are. There's no memory, so you don't have to worry about equalizing or seeing your capacity dwindle every day since you last equalized. You can happily draw them down to 20% or lower and still get thousands of charge cycles out of them. You can pull huge loads off them and the voltage sags by a couple percent, not 10-20%. You just treat them like a big dumb bucket of power -- you charge up by filling the bucket, you use it by taking power out of the bucket -- and there's nothing else to think about. It's just that easy. We will never go back to lead after living with lithium for a year.
Inverters
One of the goals of my system was to run 100% of AC loads through the inverters, and hence have no difference in anything on the boat between running off batteries and off shore power or the generator. I wanted to build the system to just leave the inverters on 100% of the time and not have to care. Leave the water heater on full time, it'll be fine, and you can shower whenever you want and not have to think about it, basically like you're living in a house.
And it's worked -- every night, Hannah and I charge our phones off outlets with integrated USB ports that are powered off the inverter, because it's easy and the tiny efficiency gains by going directly to DC don't matter to us anymore.
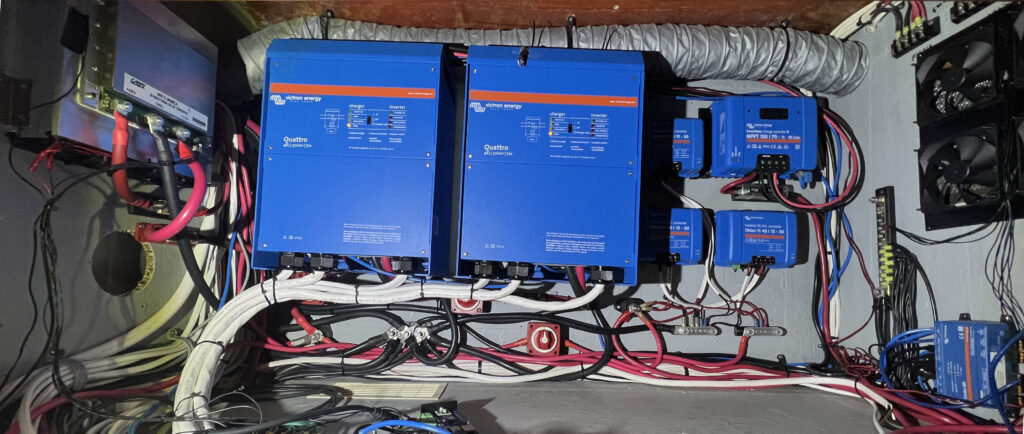
I went with two of the Victron Quattro 48/5000/70 units. The Quattros have several neat features for us:
- Auto switching between shore power and a generator, with different input power limits for each.
- Supports constant draws of 4kw each, and burst up to 8kw for a brief period of time, like for A/C compressor startup.
- Charges at up to 70A each (though with the 4kw limit, this tends to actually be more like 60A, in our experience).
- PowerAssist -- if you're on shore power/generator, and you need to pull more power than the input power gives you, it will simply augment the extra load from the batteries. When we've been stuck in situations with only a single 15A 120V outlet available on a long extension cord, PowerAssist has been awesome -- run the A/C for a while, batteries slowly drop, turn it off, batteries charge back up.
- Handles split phase power, even when we're plugged into single phase power -- one inverter charges and the other inverts, but the boat still has 240VAC available.
I was thinking there would be a lot of nuance to getting this system to work correctly in a wide variety of circumstances, but there was actually only one semi-hidden thing I had to figure out. You really need to fire up their ancient Windows-based administration software and specifically change the two inverters to disable "Switch as Group" -- this means that, if one leg has power and the other doesn't, or if the second leg isn't actually split phase (i.e. run in parallel with the first leg due to lazy marina electricians), the first inverter will still switch to using that external power, but the second one will stay as an inverter, providing that second leg of phased power for the boat. We have used this feature dozens of times at this point in the last year and a half, and it really is what makes the system set-it-and-forget-it under virtually all possible shore power electrical wackiness.
12V System
This area has undergone the most iterations since getting this boat. My original system was basically using the Port start battery as a "12V house", and using DC-DC converters to keep it charged/fed, with the converters feeding all but burst-overloads (i.e. dinghy lift, windlass, etc.) However, this system had two primary categories of downsides:
- Your "house" is your start battery -- if something goes wrong with the dc-dc converter, you're rapidly going to nuke your start battery. There was an ACR that would keep the other start battery isolated, but still, one of your motors would be dead for a while until you got enough stuff safely running to nurse it back to life.
- When you crank the motors or otherwise pull high current (windlass, etc.), the lights in the boat dim, some sensitive devices reset, etc. The DC-DC converters don't keep up with engine cranking, so the voltage sags down to ~11V, which isn't enough for many devices. I kept having to put small buck-boost converters on sensitive electronics like the router and the N2k network to keep them from dropping out every time I fired up in the morning.
I ended up wanting to move to a completely isolated 12V house setup that had nothing to do with the start batteries, and, ideally, was not, itself, battery-backed at all. I spent too much money on a 3000W 48->12V converter from Zahn, but after a couple weeks of being frustrated at how it did not respond well to transients (flushing a toilet made all the lights in the boat dim), we dinghied back to the boat one afternoon to find the entire 12V system dead with the Zahn board having completely died.
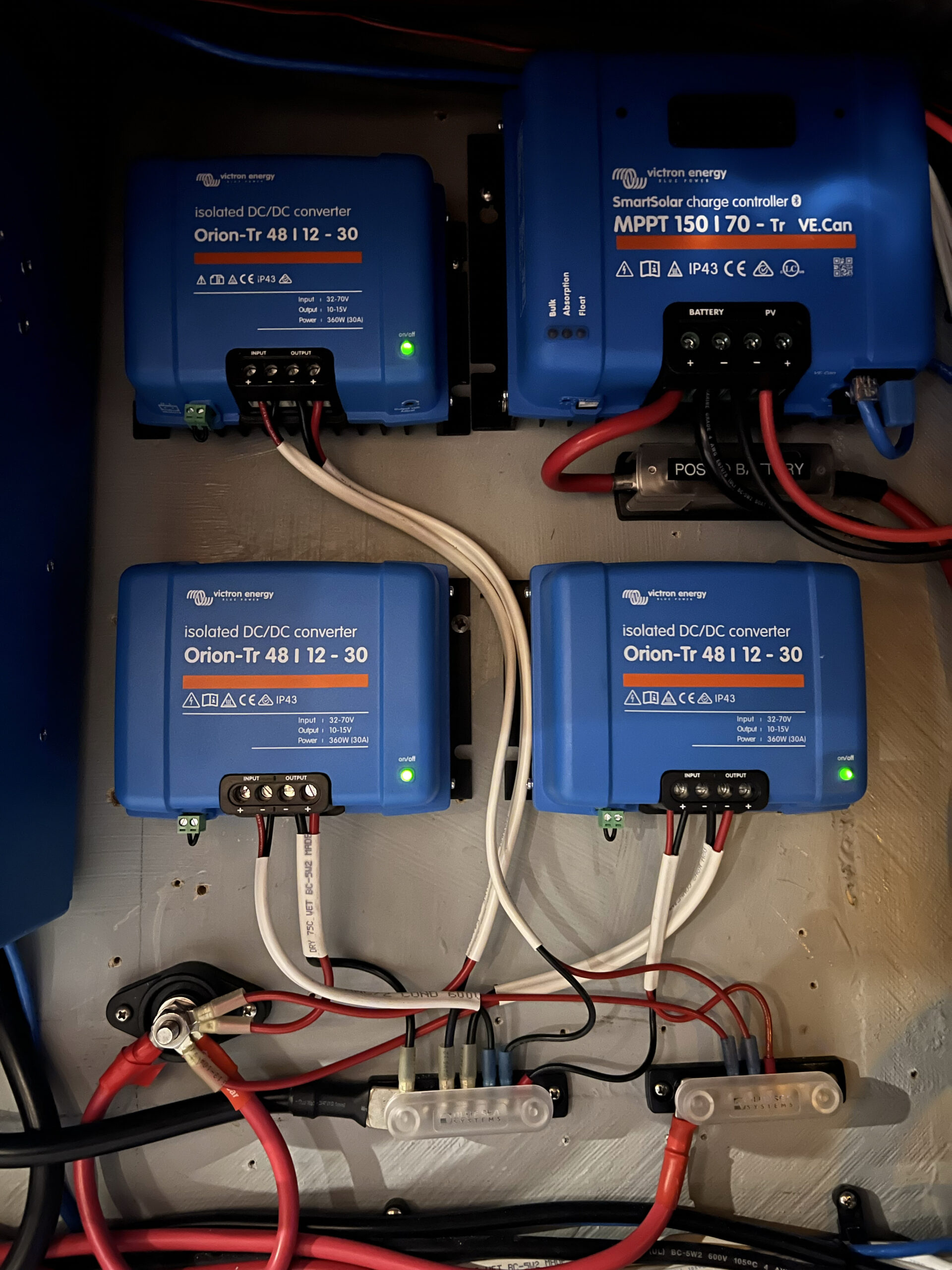
I returned the Zahn and decided to go with the tried-and-true-and-cheap Orion-Tr converters, and am now using three in parallel. That gives 90A of continuous and up to 120A of burst capacity, which is more than if we had every house-DC device on the boat turned on at the same time, and a bunch of redundancy (2 of them can die and we can still survive on a single 30A Orion-Tr). I have a backup switch to link the 12V house back to the port start battery if I need to, for some reason, which is also very helpful -- if something goes wrong in either direction, I have another 12V system waiting. It also means I can do maintenance on aspects of the power system without actually having to turn the lights off, which has come in handy a few times.
Charging from the Alternators
One of the weak points of the original power system was charging the 48V house system off the alternators. My engines don't have any sort of kit available to mount a second 48V alternator on them, and there's not really a good place for one to hack one in, so I've given up on that route and am sticking with 12V alternators so that the motor systems are still self-contained for safety/redundancy.
So, with 12V being where I was stuck, the factory "80A" (I never saw them able to put anywhere near that amount of current) alternators weren't gonna cut it. For the port side, I ended upgrading to a Balmar 94LY 210A alternator, which required a little custom hacking on the alternator bracket to make it fit, but ended up nestling in there just fine with the factory belts.
So, now I have the ability to generate something north of 200A while under way. But how can I utilize that when it's at 12V and my batteries are at 48V, and how can I make sure it only tries to pull that charging current when there's actually alternators providing that current, and not just drain the battery down?
I originally got in on an early alpha test of the upcoming WakeSpeed WS3000 bidirectional DC-DC converter, which was something that you would plug between your 12V start battery and your 48V house battery. When the 12V system was charging, it would pull current from the low side and send it to the high side to charge the house batteries. Then, when the motors were off, it would send power from the 48V high side to the low side to trickle charge any of your 12V loads (or, in my original case, "my entire 12V house load").
To control the alternator itself, I first tried using a WakeSpeed WS100, a simple 3-stage charger. However, we quickly found that, the way the WS3000 was working, it was basically fighting with the charging algorithm of the WS100 and confusing the hell out of it, since it wasn't responding like a battery would. I ended up converting to using a stupid-simple automotive adjustable-fixed-voltage regulator, which worked great for a while and I just locked to outputting 14.5V. After several months, though, that unit just magically stopped working and I switched to a Balmar BRS-2T, which is just a beefier adjustable-fixed-voltage regulator, and that's been solid ever since.
Unfortunately, after working extensively with Wakespeed for around 9 months to tweak the WS3000, we both came to the conclusion that the way they were approaching the charging algorithm needed some fundamental reworking. They were more focused on other product areas, as a tiny company, so they had to put the project on ice for a while and come back to it at some point, but it had left me without a particularly usable solution here.
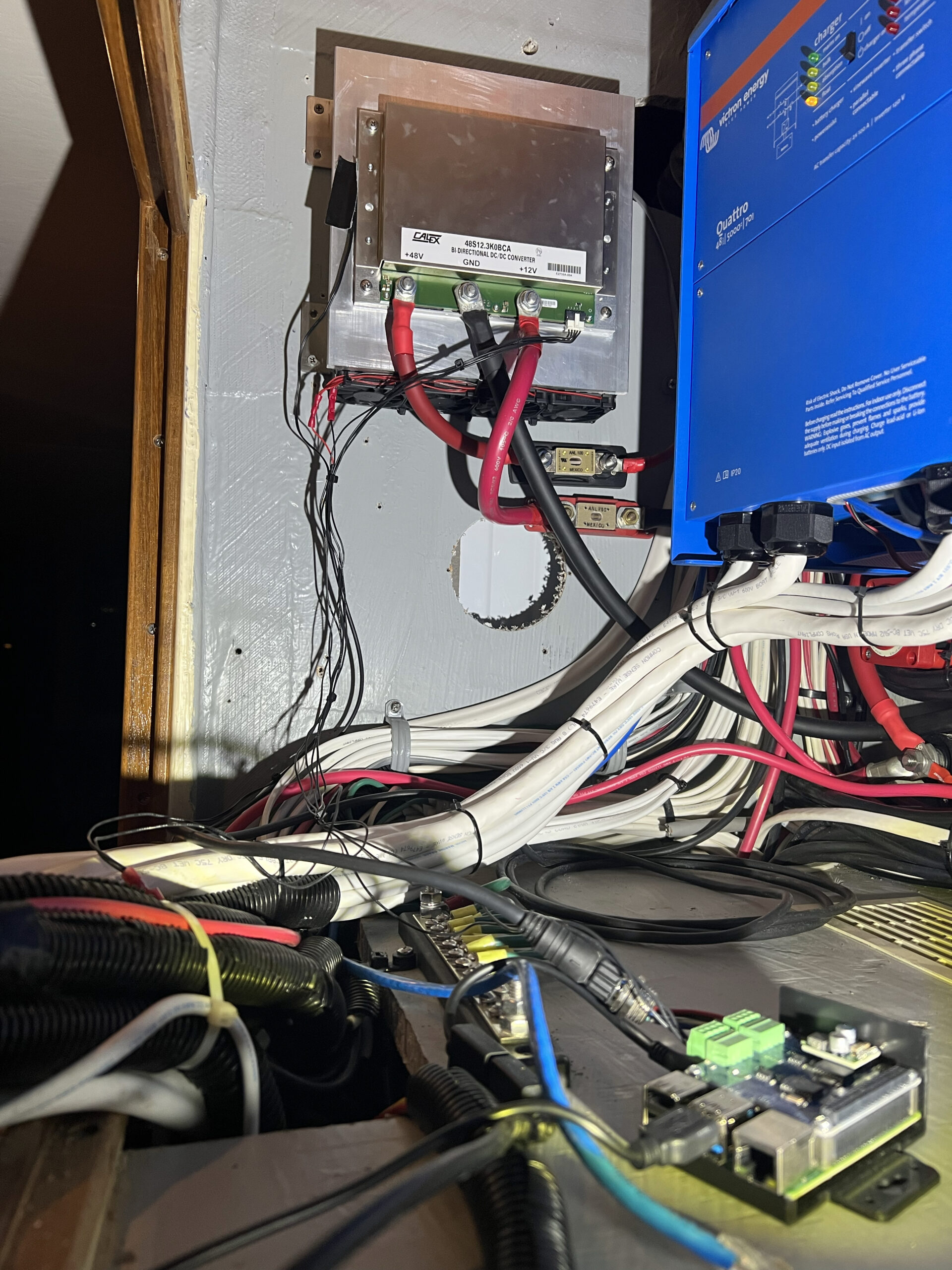
I ended up buying a Calex 3000W Bidirectional DC-DC converter board as a bit of a hail Mary and built some software to control it with a Raspberry Pi. I was thinking that a basic PID control loop would work really well to have the unit basically self-report how much current you could pull off it -- if voltage dropped below X, pull less current; if voltage goes above X, pull more current; and just keep continuously tuning. Turns out, this idea actually worked unbelievably well. The very first outing, I watched the telemetry with joy as we started out idling and watched the converter fill in the current that the diesel preheaters were using. Then as we added RPMs, the motors heated up, and the preheaters turned off, it switched to charging the high side and the current quickly jumped up and found its happy place all on its own, every time we changed RPMs.
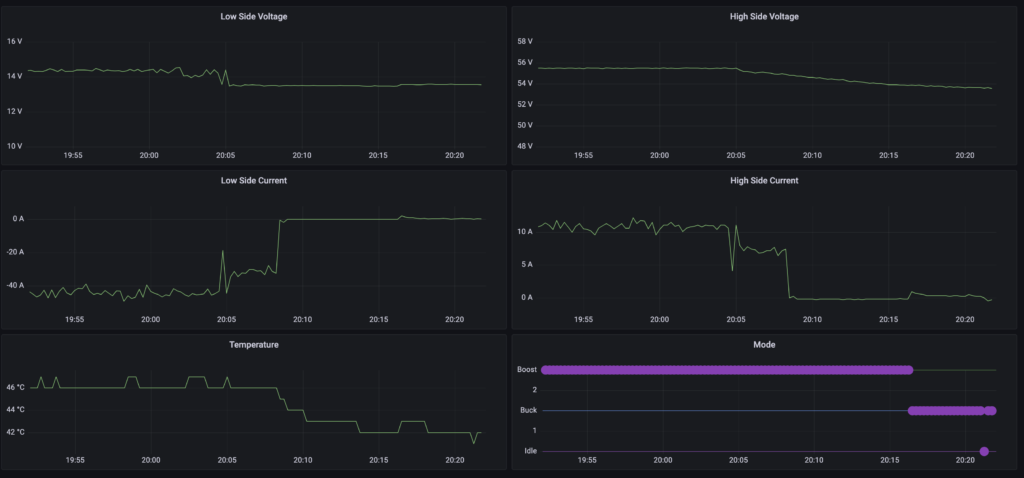
At this point, when at hull speed, I can safely pull ~180-190A from the 12V side to charge the high side at around 45A, for hours on end. When we're on plane at higher RPMs, I easily cap out the 3000W converter around 225A of low side draw. It's fully automatic, and just works, running in the background, doing its thing.
It's really a game-changer for us -- when we're moving every day, we can usually get pretty close to fully charged with every trip, combined with solar. We've put very few hours on the generator since getting this system tuned around late June, despite spending almost two full months without plugging into shore power in Maine this summer. Inquest also installed this same system and has been beta-testing the BoatKit setup and has ended up in the same place -- very little generator running required anymore.
Solar
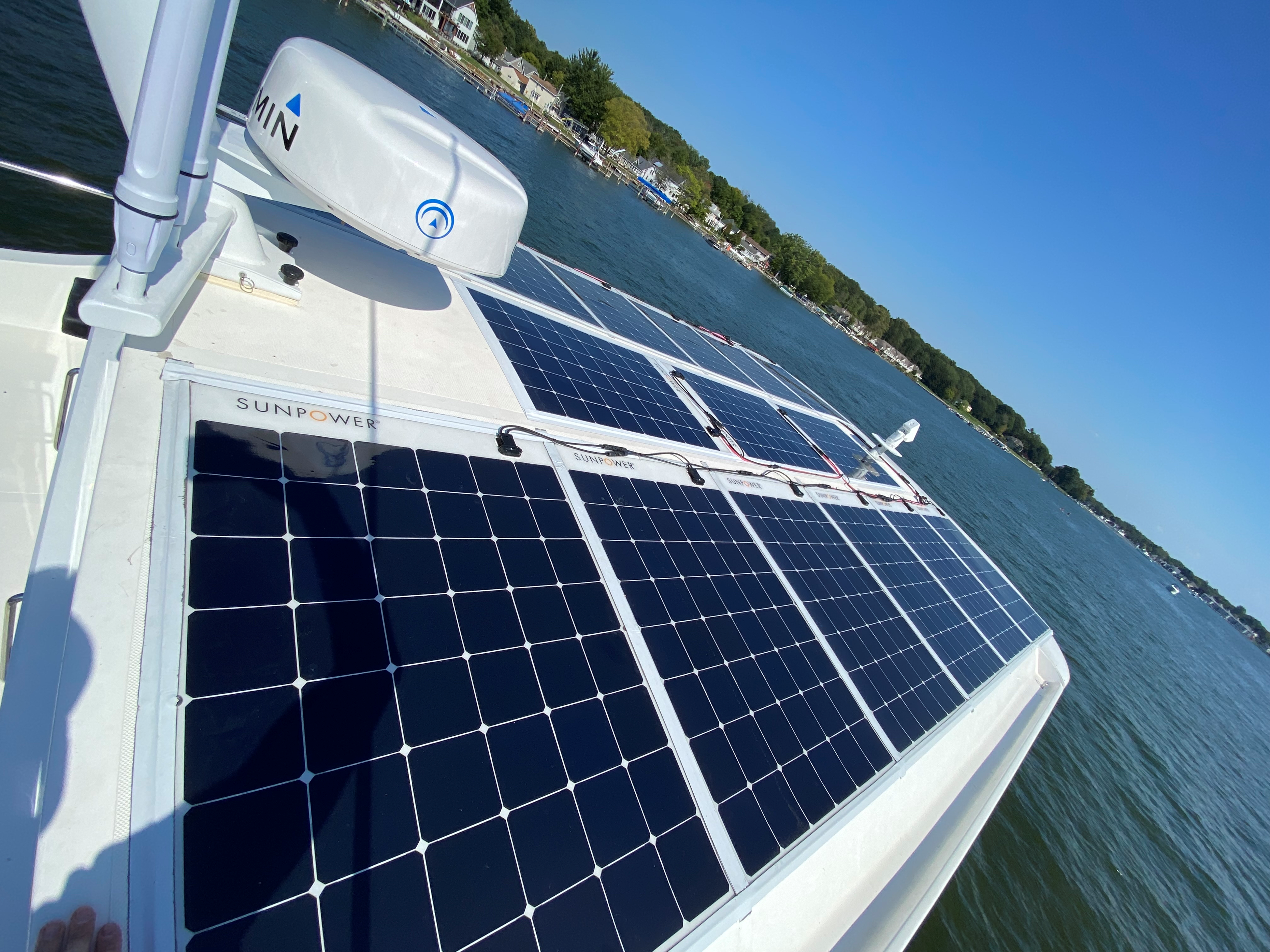
The boat originally came with four older rigid solar panels that were nominally rated at around 200W each. That just wasn't gonna cut it -- we go through a lot of power. Also, the rigid solar panels are heavy.
I'd had very good experience in the past with flexible solar panels and using Eternabond tape to hold them down to fiberglass -- the panels on our last boat survived a (non-direct-hit) hurricane just fine, and installation becomes non-permanent and super-easy. After measuring really carefully and deciding how much to work around the radar tower and FLIR on the front, I settled on putting 15 of the SunPower 170W flexible panels up top, for a nominal power capacity of 2550W. To help with shading issues, I connected them up in five parallel groups of three panels. This put the panel voltage at around 90V, with a peak current of around 28A. Better still, the total weight of the 15 flexible panels, including installation tape, is still less than the 4 rigid panels they replaced.
Getting the wiring routed semi-cleanly was not a fun endeavor, but in the end it looks pretty decent, and no one can see it from below anyway! It's all running through a single Victron 150/70A MPPT charge controller, which seems to be doing a great job, after replacing an initial buggy one with an RMA'd one that's now fine.
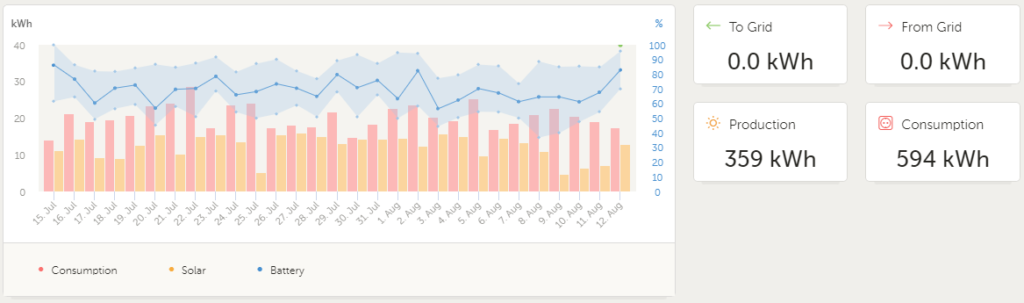
As you can see, solar is covering a significant portion of our usage. We basically only went significantly over on hot days when we had A/C on or overcast days where solar was bad. But even with running A/C regularly (it was a hot summer, even in Maine!) and all the other crazy things we do, we only averaged around an hour a day of generator usage (usually 2 hours every other day). So, the solar system is a complete success.
Generator
The boat came with a Northern Lights 12kW generator, configured to output two phases of up to 50A of 120V. It's a simple but known-to-be-reliable generator with fully analog controls and simple maintenance. This is actually a pretty perfect setup for the boat, because it matches the shore power input size (50A/240), and the two inverters want to pull around 8kW from it when charging the batteries. Running a diesel at high load is much more efficient than running at low load, so in our setup, we only run the generator when we need to charge the batteries, not just to run loads.
To keep us from having to think about generator timing, for the most part, I've set up a full autostart/stop system. Since the generator is fully manual/analog, I had to install a DynaGen TG410, which can be configured to take a single input line of high/low voltage and trigger a start/stop of the generator. It runs the preheater for a set interval, cranks, checks for voltage, etc. -- it's a full generator controller, basically.
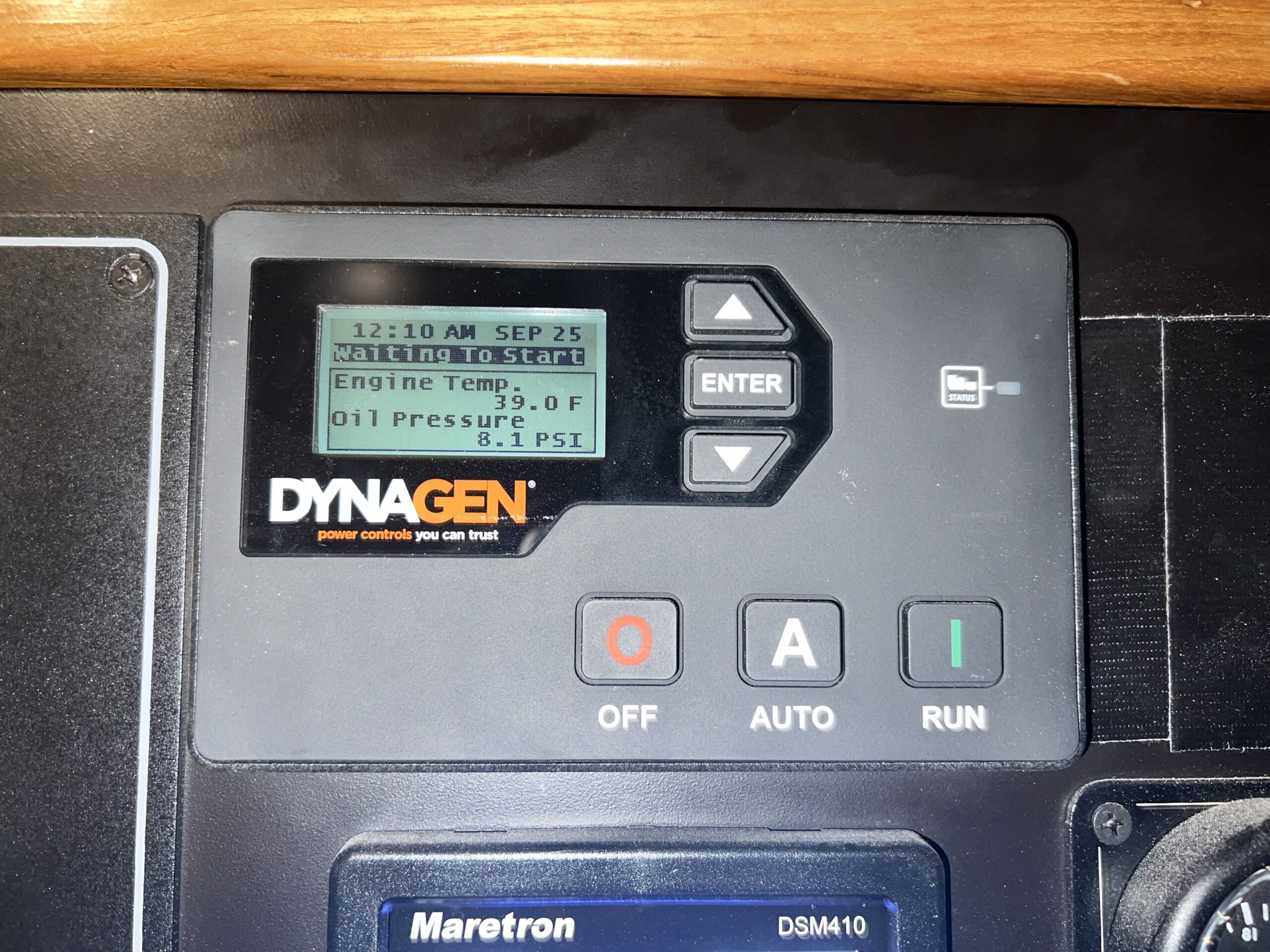
I then configured our Victron Cerbo GX's generator start/stop module with simple simple parameters -- fire up when we go below 40% SOC, stop at 85%, and during quiet hours (middle of the night) only start in an "emergency" of 20% SOC. With this setup, we basically don't have to think about charging. If it gets lowish at any point, the generator charges back up. Or we can easily manually trigger timed generator runs if we want to take control of the situation. Super helpful.
Monitoring
One of the key reasons my cabinet looks like a Victron ad is because of how nicely the whole system plays nicely together to tie into the Cerbo GX. It's a cheap box you add onto your Victron setup that you can plug a little touchscreen (Touch 50) into for your power panel, and it displays all kinds of neat info, also allowing you to control important aspects of the system. But it also connects to your boat's internet and can stream your data to the VRM online system for monitoring reasons (it can email you with issues) and digging into data in more detail.
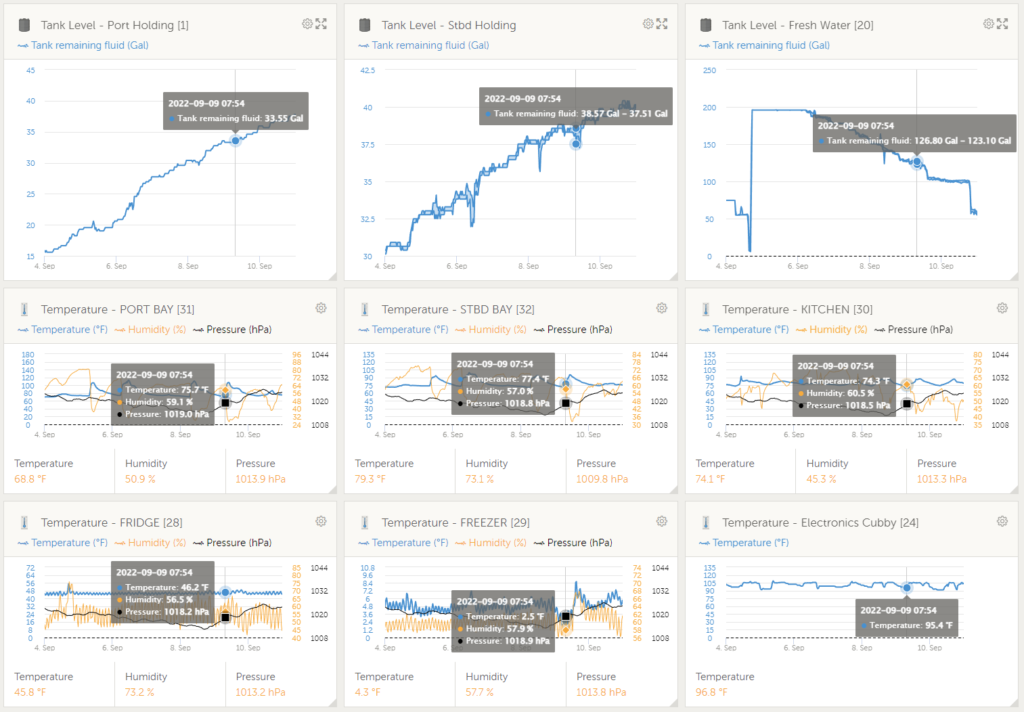
After over a year of having this system, the sheer novelty of the monitoring system has worn off, but it is still incredibly useful. Especially after installing a third party modpack called GuiMods, you can fit a pretty crazy amount of critical data on one screen. We have detailed info about the shore power and usage, what the inverters are doing, AC and DC loads at present, state of the batteries, the solar array, our pile of temperature sensors around the boat, and our tank levels.
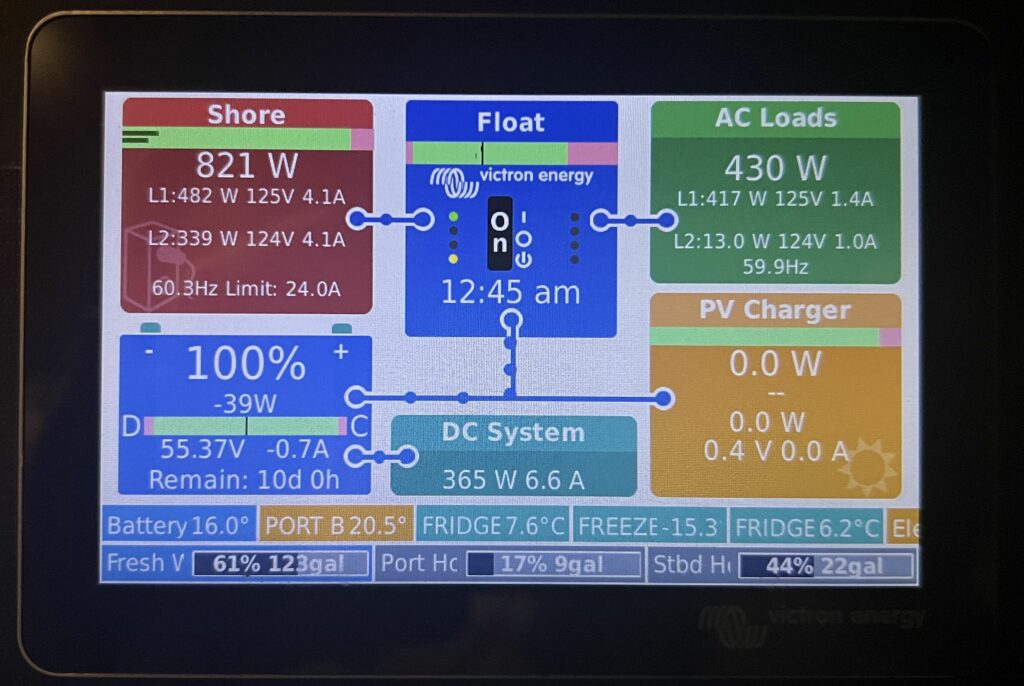
The Cerbo is really what seals the deal on the Victron suite, at least for me. The rest of the equipment also appears to be top-tier, but the Cerbo tying it all together is some sweet icing on the cake.
Summary
The system is really honed-in at this point. We can plug into any power source from 15A/120V to 50A/120-240V and the system just works. Speaking of plugging in, unless you already have a motorized shore power cord setup, just go get a SmartPlug. It's just worlds better and safer, in every way. Stop delaying or saying it's not that important. It is. Just do it.
We very rarely have to pay attention to power in the slightest unless we want to run A/C for a while, at which point we usually want to plan a generator session to make sure we start the night with pretty-full batteries to make sure we can keep the A/C on for the whole night and still be fine in the morning. Power stats are a fun thing to watch, rather than something to be carefully managed. There's always hot water and ice in the icemaker, the TV can go on whenever, and I play computer games on a desktop computer with a giant monitor all night.
The system's mature form is now designed around redundancy, with many different ways to do everything from charging the 48V batteries to powering the 12V house system to starting the engines or generator. It's being run full time on two boats that are both techy liveaboards that spend more time at anchor than in marinas.
Hopefully sometime in the next year I'll be able to get the BoatKit stuff out to the wider world so this last piece of the 48V puzzle can be accessible to the masses. But even without that piece that ties the 48V system to the motors, the rest of this setup is still something to consider if you're looking at rebuilding your power system. Hit us up with any questions!